Liquid Dye Penetrant Inspection of Aerospace Nuts
Penetrant testing (PT) is one of the oldest methods used in the field of non-destructive testing (NDT). An early form of PT called the ‘oil and whiting’ method was used by ironworkers whereby oil was used to seep into the cracks of railway tracks with capillary action and then chalk powder was applied to absorb the oil from the cracks and make them visible.
Nowadays a coloring agent is added to the oil to make it more discernible and we have industry standards which regulate materials and testing requirements, but the physics involved in the process remain largely the same.
PT is a surface inspection. Meaning that it can be used to find defects which break open to the surface such as hairline cracks and pinholes. There are two types of penetrant testing, visible and fluorescent. Fluorescent is more sensitive but requires a black light and darkened lighting for evaluation. Visible on the other hand is versatile and often employed in the field. ASTM 1417 requires all aerospace products to be inspected with fluorescent so that is what we shall use for this case study because our nuts are aerospace grade.
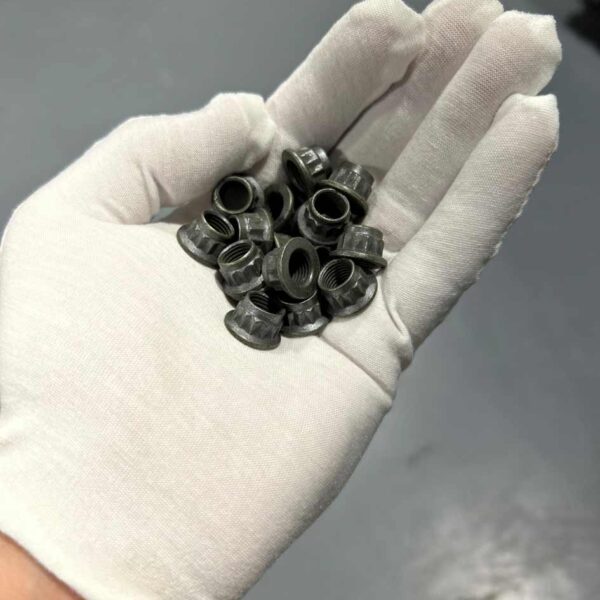
First, the parts are cleaned to prevent contamination and false results. Then penetrating oil needs to be applied to the surface of the part. This can be done by dipping, spraying, or brushing. Once the penetrant is applied, it must be allowed to dwell for a specified amount of time so that the oil can seep into surface cavities.
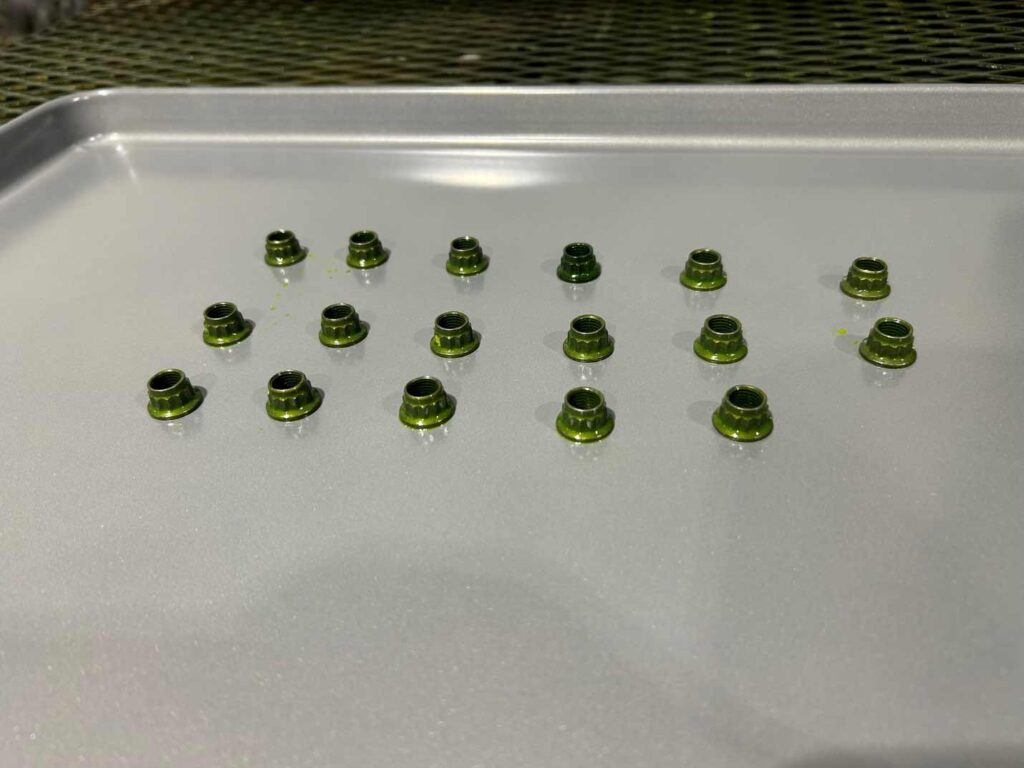
After the parts dwell for the required amount of time the excess penetrant needs to be washed away from the surface. This is done using a coarse nozzle spray at a given distance with specific water temperature and pressure allowances. We are able to monitor all of this using calibrated gauges.
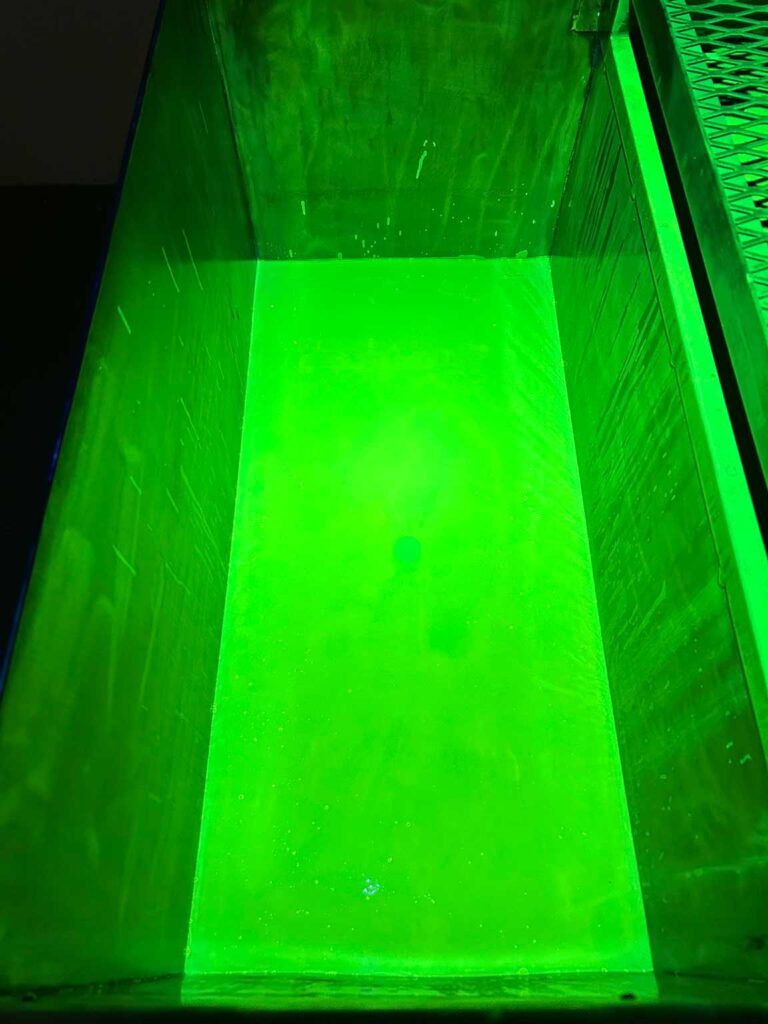
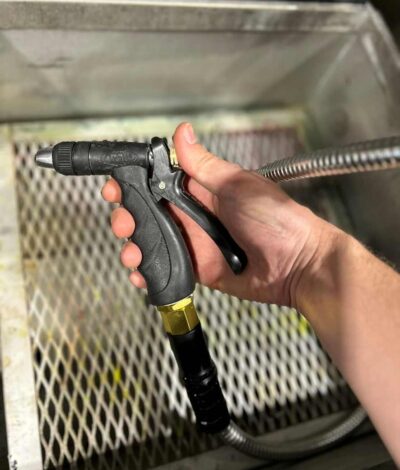
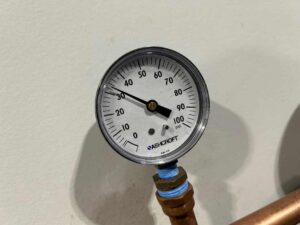
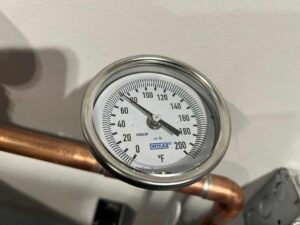
Once the excess penetrant is removed. The parts go into a dryer. After the part is dry a developer is applied. In this case a dry powder developer is used to coat the surface. Developers take advantage of a phenomenon called blotting action, where the leftover penetrant still inside of a cavity is pulled out onto the surface forming a visible indication.
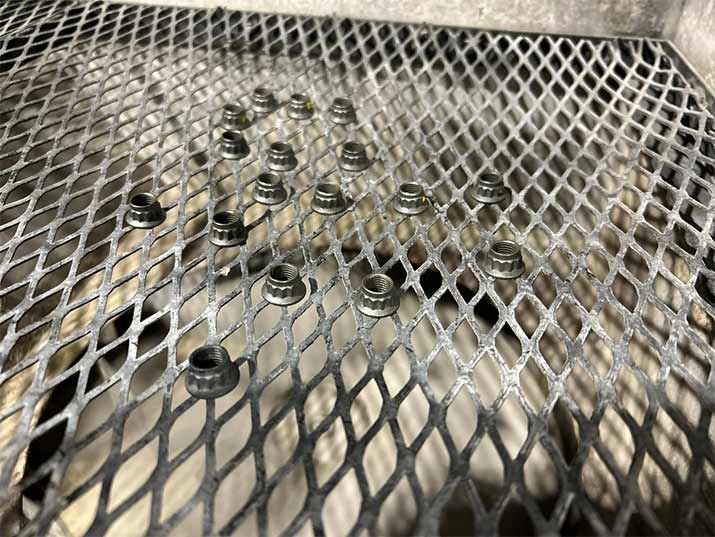
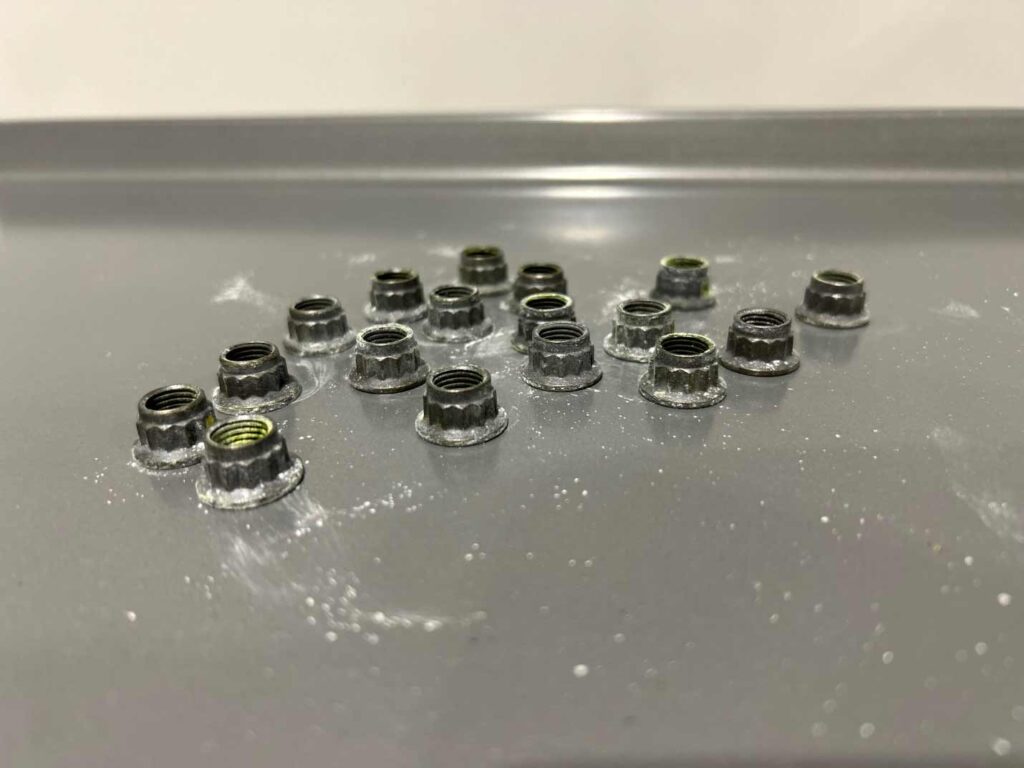
Once the developer has had sufficient time to dwell, the parts are ready for inspection. Fluorescent penetrant must be interpreted with a black light under darkened lighting.
Each part is carefully examined by a certified inspector. This individual has documented training and certifications. They are able to discern the difference between relevant, non-relevant, and false indications.
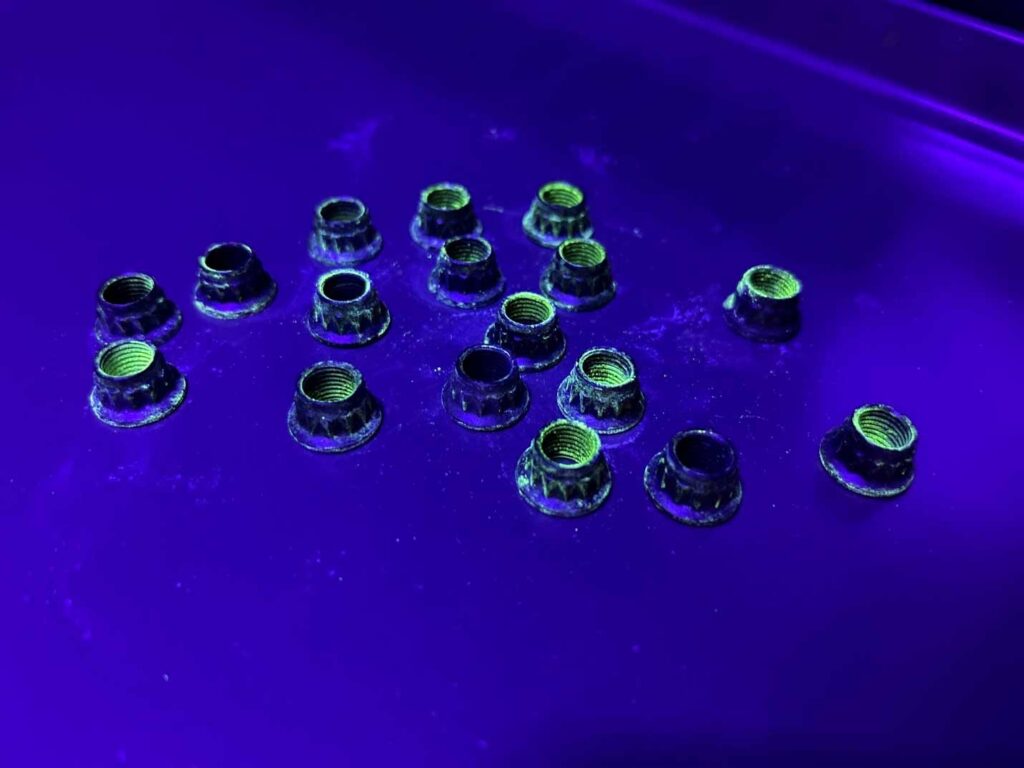
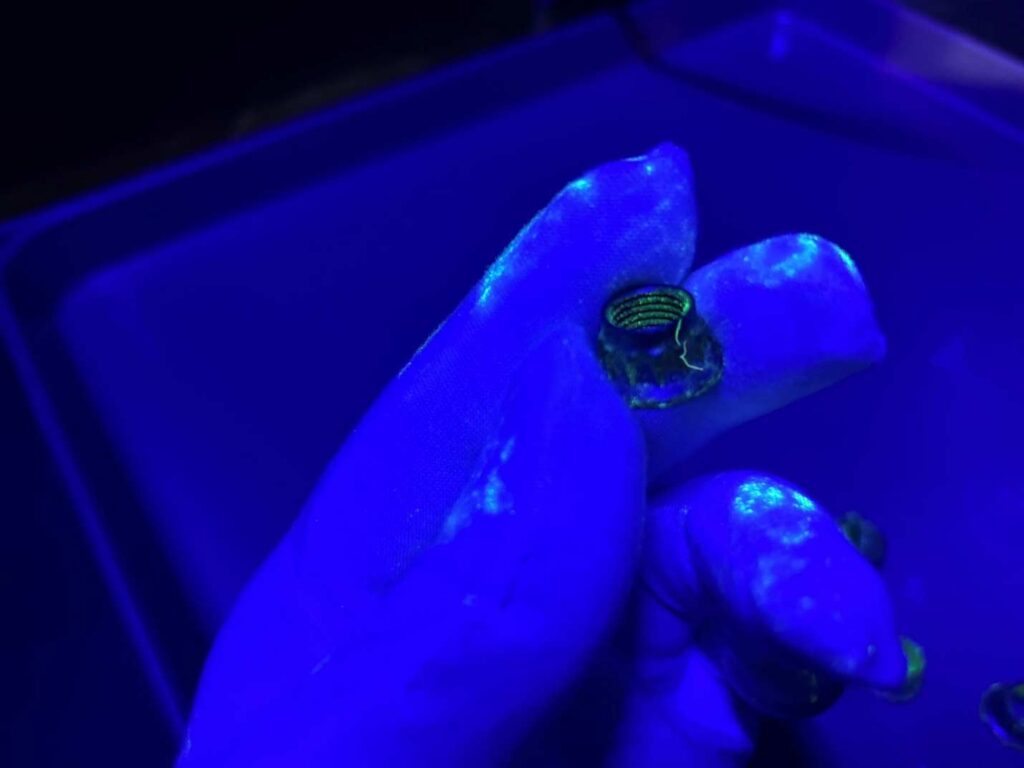
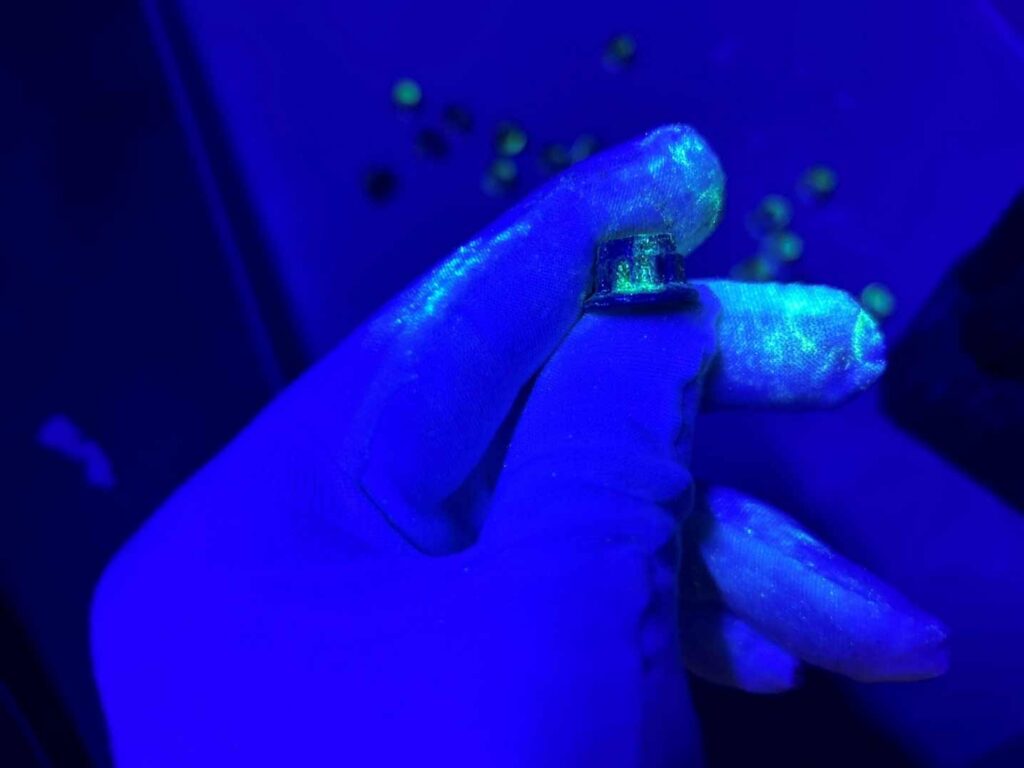
After the parts have all been inspected, a report is made. Rejected pieces are tagged and separated from the lot. The customer is notified of the findings, given a copy of the report, and the parts are returned.